Chào bạn, trong ngành cơ khí, việc sản xuất ra những sản phẩm chất lượng với chi phí hợp lý và thời gian ngắn luôn là mục tiêu hàng đầu của mọi doanh nghiệp. Để đạt được điều này, việc tối ưu hóa quy trình gia công cơ khí đóng vai trò vô cùng quan trọng. Nếu bạn đang tìm kiếm những bí quyết để cải thiện hiệu quả sản xuất, giảm thiểu lãng phí và nâng cao lợi nhuận, thì bài viết này chính là dành cho bạn. Hôm nay, chúng ta sẽ cùng nhau khám phá những cách tối ưu hóa quy trình gia công cơ khí một cách chi tiết và dễ hiểu. Hãy cùng mình bắt đầu nhé!
Giới thiệu về tầm quan trọng của việc tối ưu hóa quy trình gia công cơ khí
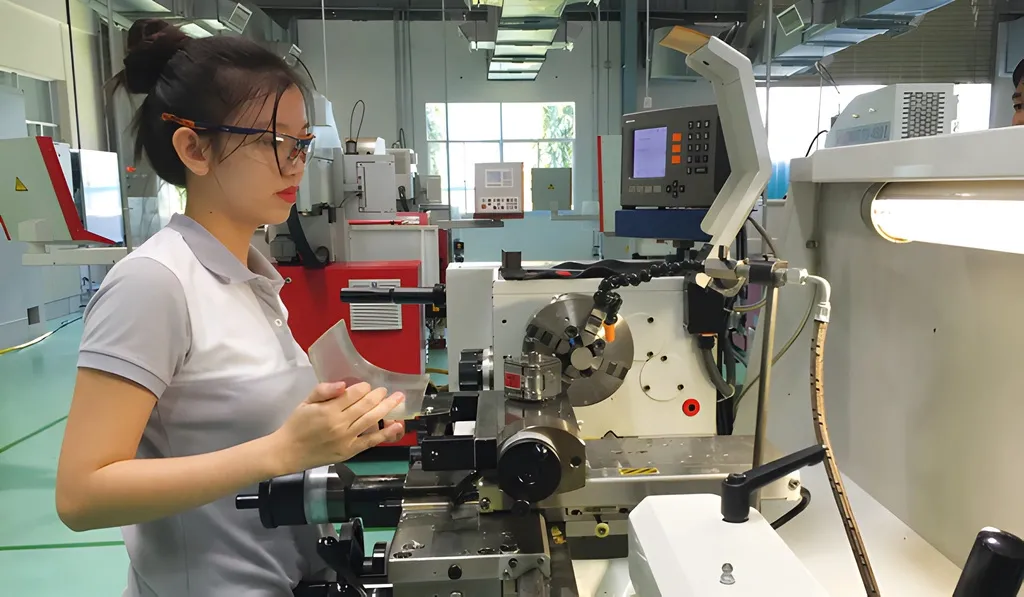
Trước khi đi sâu vào các phương pháp cụ thể, chúng ta hãy cùng nhau tìm hiểu vì sao việc tối ưu hóa quy trình gia công lại quan trọng đến vậy.
Tại sao cần tối ưu hóa quy trình gia công?
Trong môi trường cạnh tranh ngày càng khốc liệt, các doanh nghiệp cơ khí luôn phải tìm cách để nâng cao hiệu quả sản xuất và giảm chi phí. Việc tối ưu hóa quy trình gia công giúp đạt được những mục tiêu này bằng cách:
- Giảm thời gian sản xuất: Tối ưu hóa các bước trong quy trình giúp rút ngắn thời gian cần thiết để hoàn thành một sản phẩm.
- Giảm chi phí sản xuất: Loại bỏ các lãng phí về thời gian, nguyên vật liệu và nhân công giúp giảm tổng chi phí sản xuất.
- Nâng cao chất lượng sản phẩm: Quy trình được tối ưu hóa thường dẫn đến sản phẩm có độ chính xác và chất lượng cao hơn.
- Tăng năng suất: Với cùng một nguồn lực, quy trình tối ưu hóa cho phép sản xuất ra nhiều sản phẩm hơn.
- Cải thiện sự linh hoạt: Một quy trình tối ưu hóa thường dễ dàng thích ứng với những thay đổi trong yêu cầu sản xuất.
Lợi ích của việc tối ưu hóa quy trình gia công cơ khí
Việc đầu tư vào tối ưu hóa quy trình gia công cơ khí mang lại nhiều lợi ích thiết thực cho doanh nghiệp, giúp tăng cường khả năng cạnh tranh và phát triển bền vững.
Các yếu tố then chốt cần xem xét để tối ưu hóa quy trình gia công
Để tối ưu hóa quy trình gia công cơ khí một cách hiệu quả, chúng ta cần xem xét nhiều yếu tố khác nhau:
Thiết kế hướng đến khả năng gia công (Design for Manufacturability – DFM)
Ngay từ giai đoạn thiết kế sản phẩm, việc cân nhắc đến khả năng gia công là vô cùng quan trọng. Một thiết kế tốt sẽ giúp đơn giản hóa quy trình sản xuất, giảm thiểu chi phí và thời gian gia công.
- Giảm thiểu sự phức tạp của thiết kế: Tránh các hình dạng quá phức tạp hoặc các yêu cầu gia công quá khắt khe nếu không thực sự cần thiết.
- Tiêu chuẩn hóa các bộ phận và quy trình: Sử dụng các bộ phận tiêu chuẩn và áp dụng các quy trình gia công đã được kiểm chứng và tối ưu hóa.
- Lựa chọn dung sai hợp lý: Xác định dung sai phù hợp với chức năng của chi tiết, tránh đặt dung sai quá chặt gây khó khăn và tốn kém trong quá trình gia công.
Lựa chọn vật liệu phù hợp
Việc lựa chọn vật liệu không chỉ ảnh hưởng đến tính chất của sản phẩm mà còn tác động lớn đến khả năng gia công và chi phí sản xuất.
- Cân nhắc tính chất cơ học, khả năng gia công và chi phí: Chọn vật liệu có tính chất cơ học đáp ứng yêu cầu, đồng thời dễ gia công và có chi phí hợp lý.
- Sử dụng vật liệu gần với hình dạng cuối cùng của sản phẩm: Trong một số trường hợp, việc sử dụng các phương pháp như đúc hoặc rèn để tạo ra phôi có hình dạng gần với sản phẩm cuối cùng có thể giúp giảm lượng vật liệu cần loại bỏ trong quá trình gia công.
Tối ưu hóa việc lựa chọn và sử dụng dụng cụ cắt
Dụng cụ cắt đóng vai trò trực tiếp trong quá trình gia công. Việc lựa chọn và sử dụng dụng cụ phù hợp có thể giúp tăng tốc độ cắt, cải thiện chất lượng bề mặt và kéo dài tuổi thọ dụng cụ.
- Chọn dụng cụ phù hợp với vật liệu và nguyên công: Sử dụng các loại dao cắt được thiết kế đặc biệt cho từng loại vật liệu và từng nguyên công gia công cụ thể (ví dụ: dao phay mặt, dao phay ngón, dao tiện ngoài, dao tiện trong…).
- Tối ưu hóa tuổi thọ dụng cụ: Sử dụng các lớp phủ bề mặt cho dụng cụ cắt, lựa chọn thông số cắt phù hợp và thực hiện bảo trì dụng cụ định kỳ để kéo dài tuổi thọ của chúng.
- Sử dụng dụng cụ cắt hiệu suất cao: Đầu tư vào các loại dụng cụ cắt được làm từ vật liệu tiên tiến và có thiết kế tối ưu để đạt được tốc độ cắt và lượng chạy dao cao hơn.
Thiết lập các thông số gia công tối ưu
Các thông số gia công như tốc độ cắt, lượng chạy dao và chiều sâu cắt có ảnh hưởng lớn đến hiệu quả và chất lượng của quá trình gia công.
- Tốc độ cắt, lượng chạy dao, chiều sâu cắt: Thiết lập các thông số này một cách hợp lý dựa trên loại vật liệu, dụng cụ cắt và yêu cầu về chất lượng bề mặt.
- Sử dụng dữ liệu và kinh nghiệm để thiết lập thông số: Tham khảo các bảng thông số cắt do nhà sản xuất dụng cụ cung cấp và dựa vào kinh nghiệm thực tế để thiết lập các thông số ban đầu.
- Thử nghiệm và điều chỉnh thông số: Thực hiện các thử nghiệm gia công để tinh chỉnh các thông số, tìm ra bộ thông số tối ưu nhất cho từng nguyên công cụ thể.
Áp dụng công nghệ CNC và tự động hóa
Sử dụng máy CNC và các hệ thống tự động hóa là một trong những cách hiệu quả nhất để tối ưu hóa quy trình gia công cơ khí.
- Sử dụng máy CNC hiện đại: Máy CNC có độ chính xác cao, khả năng gia công phức tạp và tốc độ làm việc nhanh hơn so với máy công cụ truyền thống.
- Tự động hóa các công đoạn lặp đi lặp lại: Sử dụng các hệ thống cấp phôi tự động, hệ thống gắp phôi bằng robot để giảm sự can thiệp của con người và tăng năng suất.
- Sử dụng robot trong gia công và vận chuyển: Robot có thể được sử dụng để thực hiện các công việc gia công đơn giản, lặp đi lặp lại hoặc nguy hiểm, cũng như vận chuyển phôi và sản phẩm giữa các công đoạn.
Tối ưu hóa quy trình làm việc và bố trí nhà xưởng
Một quy trình làm việc được tổ chức tốt và một bố trí nhà xưởng hợp lý có thể giúp giảm thiểu thời gian chờ, di chuyển và các lãng phí khác.
- Sắp xếp máy móc và thiết bị hợp lý: Bố trí các máy móc và thiết bị theo trình tự của quy trình sản xuất để giảm thiểu khoảng cách di chuyển của phôi và sản phẩm.
- Giảm thiểu thời gian chờ và di chuyển: Phân tích quy trình sản xuất để xác định các điểm nghẽn và tìm cách loại bỏ hoặc giảm thiểu thời gian chờ và di chuyển không cần thiết.
- Áp dụng các nguyên tắc sản xuất tinh gọn (Lean Manufacturing): Áp dụng các nguyên tắc như 5S, Kanban, Just-in-Time (JIT) để loại bỏ lãng phí và tối ưu hóa dòng chảy sản xuất.
Nâng cao kỹ năng và đào tạo cho nhân viên
Đội ngũ nhân viên có kỹ năng cao và được đào tạo bài bản là yếu tố then chốt để vận hành và tối ưu hóa quy trình gia công cơ khí.
- Đào tạo về công nghệ mới và quy trình tối ưu: Cung cấp cho nhân viên các khóa đào tạo về công nghệ CNC mới, các quy trình gia công tiên tiến và các phương pháp tối ưu hóa.
- Khuyến khích cải tiến liên tục: Tạo một môi trường làm việc khuyến khích nhân viên đưa ra các ý tưởng cải tiến quy trình và ghi nhận những đóng góp của họ.
Kiểm soát chất lượng chặt chẽ
Việc kiểm soát chất lượng ở từng công đoạn của quy trình gia công là rất quan trọng để đảm bảo sản phẩm cuối cùng đạt yêu cầu.
- Thực hiện kiểm tra chất lượng ở từng công đoạn: Kiểm tra kích thước, hình dạng và chất lượng bề mặt của chi tiết sau mỗi công đoạn gia công.
- Sử dụng các thiết bị đo kiểm hiện đại: Đầu tư vào các thiết bị đo kiểm chính xác và hiện đại để đảm bảo kết quả kiểm tra tin cậy.
- Phân tích và xử lý các vấn đề phát sinh: Khi phát hiện các vấn đề về chất lượng, cần phân tích nguyên nhân và thực hiện các biện pháp khắc phục kịp thời.
Các công nghệ và phương pháp hỗ trợ tối ưu hóa quy trình gia công
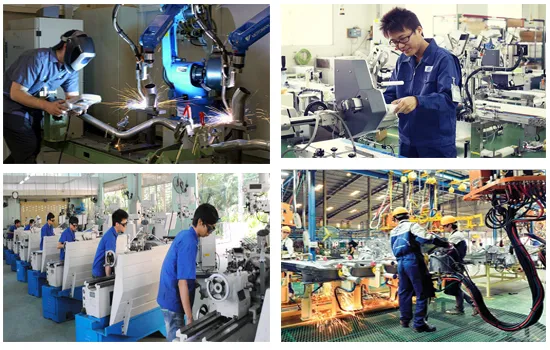
Ngoài các yếu tố trên, còn có nhiều công nghệ và phương pháp khác có thể hỗ trợ việc tối ưu hóa quy trình gia công cơ khí:
- Mô phỏng quá trình gia công (CAM Simulation): Sử dụng phần mềm CAM để mô phỏng quá trình gia công trước khi thực hiện trên máy thật, giúp phát hiện và khắc phục các vấn đề tiềm ẩn.
- Sử dụng phần mềm quản lý sản xuất (MES): Phần mềm MES giúp theo dõi và quản lý toàn bộ quá trình sản xuất, từ lập kế hoạch, điều phối công việc đến thu thập dữ liệu và phân tích hiệu suất.
- Ứng dụng Internet of Things (IoT) trong giám sát và thu thập dữ liệu: Kết nối các máy móc và thiết bị trong nhà xưởng thông qua IoT để thu thập dữ liệu thời gian thực về hiệu suất, tình trạng hoạt động, giúp đưa ra các quyết định tối ưu hóa dựa trên dữ liệu.
Kinh nghiệm thực tế về tối ưu hóa quy trình gia công cơ khí
Để bạn có thêm cái nhìn thực tế, mình xin chia sẻ một vài câu chuyện thành công về việc tối ưu hóa quy trình gia công cơ khí:
Câu chuyện 1: Giảm thời gian gia công bằng cách tối ưu hóa thông số cắt
Anh Hùng, kỹ sư tại một xưởng gia công cơ khí, đã dành thời gian nghiên cứu và thử nghiệm các thông số cắt khác nhau cho một chi tiết cụ thể. Sau khi tìm ra bộ thông số tối ưu, anh đã giảm được thời gian gia công cho chi tiết đó xuống 30%, giúp tăng đáng kể năng suất của xưởng.
Câu chuyện 2: Tăng năng suất nhờ tự động hóa quá trình cấp phôi
Một công ty sản xuất phụ tùng ô tô đã đầu tư vào một hệ thống cấp phôi tự động cho các máy CNC của họ. Nhờ đó, máy có thể hoạt động liên tục mà không cần công nhân đứng máy cấp phôi, giúp tăng năng suất lên gấp đôi.
Câu chuyện 3: Cải thiện chất lượng sản phẩm nhờ thiết kế lại chi tiết
Một công ty sản xuất thiết bị y tế đã gặp vấn đề về chất lượng bề mặt của một chi tiết quan trọng. Sau khi phân tích, họ nhận thấy nguyên nhân đến từ thiết kế của chi tiết gây khó khăn cho quá trình gia công. Bằng cách thiết kế lại chi tiết, họ đã cải thiện đáng kể chất lượng bề mặt và giảm thiểu phế phẩm.
Những thách thức thường gặp khi tối ưu hóa quy trình gia công
Mặc dù mang lại nhiều lợi ích, việc tối ưu hóa quy trình gia công cơ khí cũng có thể gặp một số thách thức:
- Chi phí đầu tư ban đầu: Việc đầu tư vào máy móc, thiết bị và phần mềm mới có thể đòi hỏi một khoản chi phí ban đầu đáng kể.
- Sự kháng cự thay đổi từ nhân viên: Một số nhân viên có thể không muốn thay đổi các quy trình làm việc quen thuộc.
- Thiếu dữ liệu và công cụ phân tích: Để tối ưu hóa hiệu quả, cần có dữ liệu chính xác về hiệu suất và các công cụ phân tích phù hợp.
Lời khuyên cho các doanh nghiệp muốn tối ưu hóa quy trình gia công cơ khí
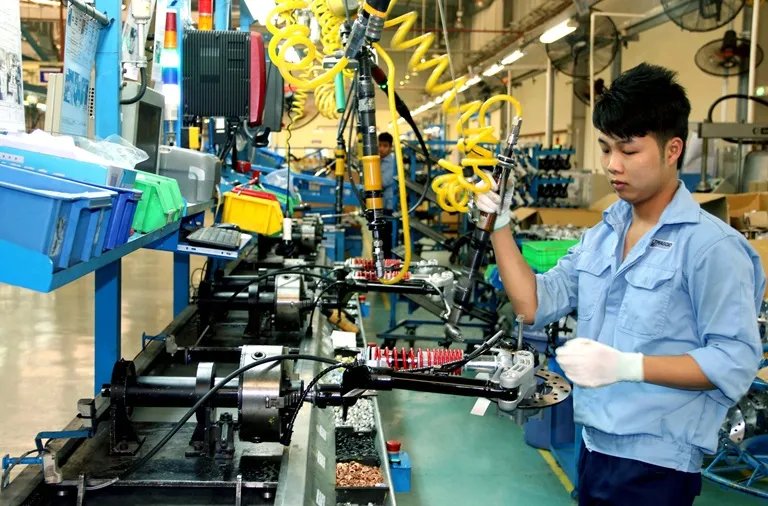
Nếu doanh nghiệp của bạn đang muốn tối ưu hóa quy trình gia công cơ khí, đây là một vài lời khuyên:
- Bắt đầu từ những vấn đề nhỏ và cụ thể: Thay vì cố gắng thay đổi mọi thứ cùng một lúc, hãy tập trung vào việc giải quyết các vấn đề cụ thể đang gây ra lãng phí hoặc làm chậm quá trình sản xuất.
- Thu thập và phân tích dữ liệu: Dựa trên dữ liệu thực tế để đưa ra các quyết định tối ưu hóa.
- Tham khảo ý kiến của nhân viên: Những người trực tiếp tham gia vào quy trình thường có những hiểu biết sâu sắc và các ý tưởng cải tiến giá trị.
- Thực hiện các thử nghiệm và đánh giá kết quả: Đừng ngại thử nghiệm các phương pháp mới và đánh giá hiệu quả của chúng.
- Kiên trì và cải tiến liên tục: Tối ưu hóa quy trình là một quá trình liên tục, đòi hỏi sự kiên trì và cam kết cải tiến không ngừng.
Kết luận về tầm quan trọng và các bước để tối ưu hóa quy trình gia công cơ khí
Tối ưu hóa quy trình gia công cơ khí là một yếu tố then chốt để các doanh nghiệp nâng cao hiệu quả sản xuất, giảm chi phí và tăng cường khả năng cạnh tranh. Bằng cách xem xét kỹ lưỡng các yếu tố như thiết kế, vật liệu, dụng cụ cắt, thông số gia công, tự động hóa, quy trình làm việc, kỹ năng nhân viên và kiểm soát chất lượng, cùng với việc áp dụng các công nghệ hỗ trợ, các doanh nghiệp có thể đạt được những cải thiện đáng kể trong quy trình sản xuất của mình. Chúc bạn thành công trên con đường tối ưu hóa quy trình gia công cơ khí!