Chào bạn, trong ngành cơ khí, việc bảo vệ và nâng cao tính năng của các chi tiết kim loại là vô cùng quan trọng. Một trong những phương pháp hiệu quả và phổ biến để đạt được điều này chính là công nghệ mạ điện. Bạn có bao giờ thắc mắc mạ điện là gì, nó được thực hiện như thế nào và có những ứng dụng gì trong thực tế không? Hôm nay, chúng ta sẽ cùng nhau khám phá sâu hơn về công nghệ mạ điện trong cơ khí, từ quy trình cơ bản, các loại mạ phổ biến đến những ứng dụng và lợi ích mà nó mang lại nhé!
Giới thiệu tổng quan về công nghệ mạ điện
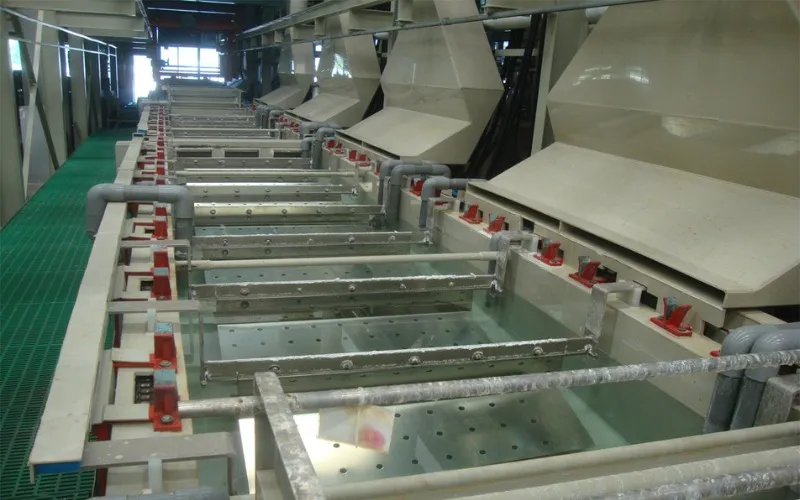
Để bắt đầu, chúng ta hãy cùng nhau làm rõ những khái niệm cơ bản về công nghệ mạ điện.
Mạ điện là gì? Định nghĩa dễ hiểu
Mạ điện (Electroplating) là một quá trình sử dụng dòng điện để phủ một lớp kim loại mỏng lên bề mặt của một vật liệu dẫn điện khác. Mục đích của việc mạ điện thường là để cải thiện các đặc tính của bề mặt như khả năng chống ăn mòn, độ cứng, độ bền, tính dẫn điện hoặc đơn giản là để tăng tính thẩm mỹ cho sản phẩm. Bạn có thể hình dung nó giống như việc “mặc” một lớp áo kim loại mới cho vật liệu vậy.
Vai trò quan trọng của mạ điện trong ngành cơ khí
Trong ngành cơ khí, công nghệ mạ điện đóng một vai trò vô cùng quan trọng. Nó giúp bảo vệ các chi tiết máy móc khỏi sự ăn mòn của môi trường, tăng tuổi thọ và độ bền cho sản phẩm. Ngoài ra, mạ điện còn được sử dụng để cải thiện các tính năng kỹ thuật khác của bề mặt kim loại, đáp ứng các yêu cầu khắt khe trong nhiều ứng dụng khác nhau.
Lịch sử phát triển của công nghệ mạ điện
Mặc dù có vẻ là một công nghệ hiện đại, nhưng mạ điện đã có lịch sử phát triển khá lâu đời. Các bằng chứng khảo cổ cho thấy con người đã biết đến các hình thức mạ kim loại từ hàng ngàn năm trước. Tuy nhiên, quá trình mạ điện hiện đại dựa trên nguyên lý điện phân chỉ thực sự được phát triển vào đầu thế kỷ 19 nhờ những khám phá quan trọng trong lĩnh vực điện hóa học.
Nguyên lý cơ bản của quá trình mạ điện
Quá trình mạ điện dựa trên nguyên lý điện phân, diễn ra trong một bể mạ điện chứa dung dịch điện ly. Dưới đây là các bước cơ bản:
Chuẩn bị bề mặt vật liệu
Đây là bước quan trọng đầu tiên để đảm bảo lớp mạ bám dính tốt và có chất lượng cao. Bề mặt vật liệu cần được làm sạch hoàn toàn khỏi bụi bẩn, dầu mỡ, oxit kim loại và các tạp chất khác. Các phương pháp làm sạch thường bao gồm tẩy dầu mỡ, tẩy gỉ, rửa bằng nước và đôi khi là các xử lý hóa học đặc biệt.
Thiết lập bể mạ điện
Bể mạ điện chứa dung dịch điện ly (thường là dung dịch muối của kim loại cần mạ), anot (thường là kim loại cần mạ hoặc vật liệu trơ) và catot (chính là vật liệu cần mạ). Anot và catot được kết nối với nguồn điện một chiều.
Quá trình điện phân
Khi dòng điện một chiều chạy qua dung dịch điện ly, các ion kim loại từ anot sẽ di chuyển về phía catot. Tại catot, các ion kim loại này sẽ nhận electron và kết tủa thành lớp kim loại mỏng bám trên bề mặt vật liệu cần mạ. Đồng thời, tại anot, kim loại sẽ bị hòa tan vào dung dịch điện ly, duy trì nồng độ ion kim loại trong bể mạ.
Rửa và sấy khô sản phẩm
Sau khi quá trình mạ điện hoàn tất, sản phẩm sẽ được lấy ra khỏi bể mạ, rửa sạch để loại bỏ các hóa chất còn sót lại và sau đó được sấy khô.
Các yếu tố ảnh hưởng đến chất lượng lớp mạ điện
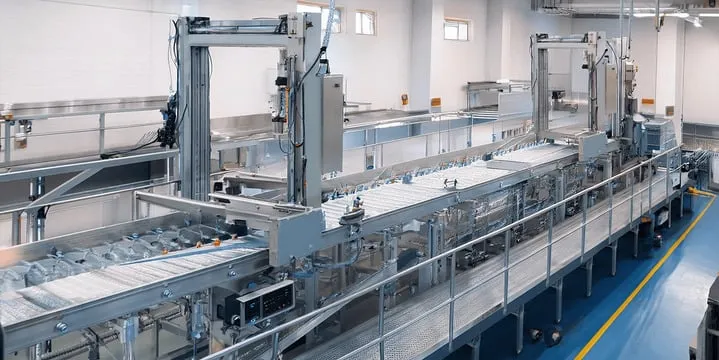
Chất lượng của lớp mạ điện chịu ảnh hưởng của nhiều yếu tố khác nhau:
Thành phần dung dịch điện ly
Loại muối kim loại, nồng độ, độ pH, các chất phụ gia trong dung dịch điện ly đều có ảnh hưởng lớn đến tốc độ mạ, độ bám dính, độ dày, độ bóng và độ cứng của lớp mạ.
Mật độ dòng điện
Mật độ dòng điện (cường độ dòng điện trên một đơn vị diện tích bề mặt) ảnh hưởng đến tốc độ kết tủa kim loại. Mật độ dòng điện quá cao có thể dẫn đến lớp mạ xốp, không đều hoặc bị cháy.
Nhiệt độ bể mạ
Nhiệt độ của dung dịch điện ly ảnh hưởng đến độ hòa tan của muối kim loại, độ dẫn điện của dung dịch và tốc độ phản ứng điện hóa.
Thời gian mạ
Thời gian mạ quyết định độ dày của lớp mạ. Thời gian mạ càng lâu thì lớp mạ càng dày.
Chuẩn bị bề mặt
Như đã nói ở trên, việc chuẩn bị bề mặt kỹ lưỡng là yếu tố then chốt để đảm bảo lớp mạ bám dính tốt và không bị bong tróc.
Các loại mạ điện phổ biến trong ngành cơ khí
Trong ngành cơ khí, có nhiều loại mạ điện được sử dụng tùy thuộc vào mục đích và yêu cầu cụ thể:
Mạ kẽm (Zinc Plating)
Đây là loại mạ điện phổ biến nhất, chủ yếu được sử dụng để bảo vệ thép và sắt khỏi sự ăn mòn. Lớp mạ kẽm tạo thành một lớp bảo vệ thụ động, ngăn chặn sự tiếp xúc của kim loại nền với môi trường bên ngoài.
Mạ niken (Nickel Plating)
Mạ niken tạo ra lớp phủ có độ cứng cao, khả năng chống mài mòn tốt và bề mặt sáng bóng. Nó thường được sử dụng để tăng độ bền và tính thẩm mỹ cho các chi tiết máy.
Mạ crom (Chromium Plating)
Mạ crom tạo ra lớp phủ rất cứng, chống mài mòn và ăn mòn tuyệt vời, đồng thời có bề mặt sáng bóng. Nó thường được sử dụng cho các chi tiết chịu ma sát lớn như piston, trục khuỷu và các dụng cụ cắt.
Mạ đồng (Copper Plating)
Mạ đồng thường được sử dụng làm lớp mạ trung gian để cải thiện độ bám dính của các lớp mạ khác (ví dụ như niken hoặc crom) hoặc để tăng tính dẫn điện.
Mạ thiếc (Tin Plating)
Mạ thiếc được sử dụng chủ yếu để bảo vệ các chi tiết khỏi sự ăn mòn và để cải thiện khả năng hàn. Nó thường được ứng dụng trong ngành điện tử và thực phẩm.
Mạ vàng (Gold Plating)
Mạ vàng thường được sử dụng để tăng tính dẫn điện và khả năng chống ăn mòn, đặc biệt trong các ứng dụng điện tử và viễn thông. Ngoài ra, nó còn được sử dụng cho mục đích trang trí.
Mạ bạc (Silver Plating)
Tương tự như mạ vàng, mạ bạc cũng được sử dụng để tăng tính dẫn điện và khả năng chống ăn mòn. Nó thường được ứng dụng trong các thiết bị điện và điện tử cao cấp.
Ứng dụng rộng rãi của công nghệ mạ điện trong cơ khí
Công nghệ mạ điện có vô số ứng dụng trong ngành cơ khí, có thể kể đến như:
Chống ăn mòn và bảo vệ bề mặt
Đây là ứng dụng phổ biến nhất của mạ điện, giúp tăng tuổi thọ và độ bền cho các chi tiết máy móc hoạt động trong môi trường khắc nghiệt.
Tăng độ cứng và độ bền
Các lớp mạ như niken và crom có độ cứng cao, giúp tăng khả năng chống mài mòn và va đập cho bề mặt chi tiết.
Cải thiện tính dẫn điện
Mạ vàng và mạ bạc được sử dụng để tăng khả năng dẫn điện cho các tiếp điểm điện và các linh kiện điện tử.
Tạo lớp phủ trang trí
Mạ crom, niken, vàng, bạc được sử dụng để tạo ra các bề mặt sáng bóng, tăng tính thẩm mỹ cho sản phẩm.
Phục hồi kích thước chi tiết bị mài mòn
Trong một số trường hợp, mạ điện có thể được sử dụng để phục hồi kích thước của các chi tiết máy bị mài mòn nhẹ.
Ưu điểm và nhược điểm của công nghệ mạ điện
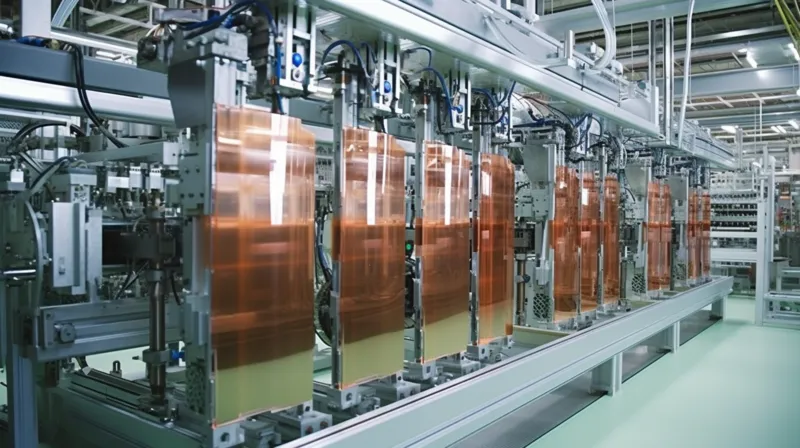
Giống như mọi công nghệ khác, mạ điện cũng có những ưu điểm và nhược điểm riêng:
Ưu điểm
- Cải thiện các đặc tính bề mặt của vật liệu nền một cách hiệu quả.
- Có thể mạ được nhiều loại kim loại khác nhau lên nhiều loại vật liệu nền.
- Chi phí tương đối thấp so với một số phương pháp xử lý bề mặt khác.
- Có thể kiểm soát độ dày của lớp mạ một cách chính xác.
- Ứng dụng rộng rãi trong nhiều ngành công nghiệp.
Nhược điểm
- Quá trình mạ điện có thể tạo ra các chất thải độc hại, cần được xử lý đúng quy trình.
- Chất lượng lớp mạ phụ thuộc nhiều vào quá trình chuẩn bị bề mặt và các thông số kỹ thuật.
- Độ bám dính của lớp mạ có thể bị ảnh hưởng bởi các yếu tố bên ngoài.
- Không phù hợp với các chi tiết quá lớn hoặc có hình dạng quá phức tạp trong một số trường hợp.
Quy trình mạ điện cơ bản trong thực tế
Để bạn hình dung rõ hơn về quá trình mạ điện, mình xin mô tả một quy trình mạ điện kẽm cơ bản:
Bước 1: Chuẩn bị bề mặt
Các chi tiết thép cần mạ kẽm sẽ được tẩy dầu mỡ bằng dung dịch kiềm nóng, sau đó được rửa sạch bằng nước. Tiếp theo, chúng sẽ được tẩy gỉ bằng dung dịch axit clohydric hoặc axit sulfuric, và lại được rửa sạch.
Bước 2: Gá lắp sản phẩm
Các chi tiết sau khi đã được làm sạch sẽ được gá lên các móc treo hoặc đặt trong các thùng quay (đối với các chi tiết nhỏ) để đưa vào bể mạ.
Bước 3: Tiến hành mạ điện
Các chi tiết được nhúng vào bể mạ kẽm chứa dung dịch điện ly kẽm clorua hoặc kẽm sunfat. Anot thường là các tấm kẽm nguyên chất. Dòng điện một chiều được cấp vào bể mạ trong một khoảng thời gian nhất định, tùy thuộc vào độ dày lớp mạ mong muốn.
Bước 4: Xử lý sau mạ
Sau khi mạ xong, các chi tiết được lấy ra, rửa sạch bằng nước để loại bỏ dung dịch điện ly còn bám trên bề mặt. Sau đó, chúng có thể được thụ động hóa bằng dung dịch cromat để tăng khả năng chống ăn mòn và tạo màu sắc đặc trưng cho lớp mạ kẽm (ví dụ như màu trắng xanh, màu vàng). Cuối cùng, các chi tiết được sấy khô.
Bước 5: Kiểm tra chất lượng
Lớp mạ kẽm sẽ được kiểm tra về độ dày, độ bám dính, độ bóng và khả năng chống ăn mòn theo các tiêu chuẩn kỹ thuật.
Những lưu ý quan trọng khi thực hiện mạ điện
Khi thực hiện quá trình mạ điện, cần đặc biệt chú ý đến các yếu tố sau:
An toàn lao động
Mạ điện sử dụng các hóa chất độc hại và dòng điện, vì vậy cần tuân thủ nghiêm ngặt các quy tắc an toàn lao động, sử dụng đồ bảo hộ cá nhân đầy đủ (găng tay, kính bảo hộ, khẩu trang…).
Xử lý chất thải
Nước thải và các chất thải từ quá trình mạ điện chứa nhiều kim loại nặng và hóa chất độc hại, cần được xử lý theo đúng quy định của pháp luật về bảo vệ môi trường.
Kiểm soát chất lượng
Cần kiểm soát chặt chẽ các thông số kỹ thuật trong quá trình mạ điện để đảm bảo chất lượng lớp mạ đồng đều và đáp ứng yêu cầu.
Câu chuyện thực tế về ứng dụng mạ điện trong cơ khí
Để bạn thấy rõ hơn về ứng dụng của mạ điện trong cơ khí, mình xin chia sẻ một vài ví dụ:
Ví dụ 1: Mạ crom cho piston xi lanh thủy lực
Trong các hệ thống thủy lực, piston và xi lanh thường xuyên phải chịu ma sát và áp lực lớn. Việc mạ một lớp crom dày lên bề mặt piston giúp tăng độ cứng, khả năng chống mài mòn và chống ăn mòn, kéo dài tuổi thọ của hệ thống.
Ví dụ 2: Mạ kẽm cho các chi tiết bulong, ốc vít
Các chi tiết bulong, ốc vít thường được sử dụng trong nhiều môi trường khác nhau, bao gồm cả môi trường ẩm ướt và có tính ăn mòn cao. Việc mạ kẽm giúp bảo vệ các chi tiết này khỏi bị gỉ sét, đảm bảo độ bền và khả năng kết nối của chúng.
Xu hướng phát triển của công nghệ mạ điện trong tương lai
Công nghệ mạ điện đang không ngừng phát triển với nhiều xu hướng mới, bao gồm việc nghiên cứu và ứng dụng các loại dung dịch mạ thân thiện với môi trường hơn, phát triển các quy trình mạ tiên tiến để tạo ra các lớp phủ có tính năng đặc biệt (ví dụ như mạ nano, mạ hợp kim) và tối ưu hóa quy trình sản xuất để giảm chi phí và tăng hiệu quả.
Lời kết về tầm quan trọng của công nghệ mạ điện
Công nghệ mạ điện đóng một vai trò không thể thiếu trong ngành cơ khí, giúp nâng cao chất lượng, độ bền và tính thẩm mỹ cho các sản phẩm. Việc hiểu rõ về quy trình, các loại mạ phổ biến và những ứng dụng của nó sẽ giúp bạn có cái nhìn toàn diện hơn về công nghệ quan trọng này. Hy vọng bài viết này đã mang lại cho bạn những thông tin hữu ích và thú vị!